About the plastic injection system?
Injection molding is an engineering technology. It involves changing plastics into useful products with its original properties. The important process conditions for injection molding are the temperature, pressure and corresponding action time that affect plasticizing flow and cooling.
A.Temperature Control
1.Feed cylinder temperature:Temperatures that need be controlled during injection molding are feed cylinder temperature, nozzle temperature, and mold temperature. The first two temperatures mainly affect plastics’ plasticizing and flowing, and the third one mainly affects plastics’ flowing and cooling. Every kind of plastics has different flow temperature. Flow temperature and decomposition temperature for same kind of plastics with different origin or brand also have differences because of different average molecular weight and molecular weight distribution. The plasticizing process of plastics in different types of injection machines is also different, so the corresponding cylinder temperatures are varied.
2.Nozzle temperature:
nozzle temperature usually should be slightly lower than the highest temperature of feed cylinder. This is for avoiding that melt in straight through nozzle may cause material drooling phenomenon. But the nozzle temperature cannot be too low. Otherwise it will lead to untimely condensing of melt which will block nozzle, or that untimely condensing material enters cavity affecting product properties.
3.Mold temperature:
mold temperature has a great affect on product intrinsic properties and apparent mass. Mold temperature depends on plastics’ crystallinity, requirements on product size, structure and properties, and other process conditions (melt temperature, injection speed, injection pressure and molding cycle).
B.Pressure Control: pressures during injection molding include plasticizing pressure and injection pressure. They directly affect plastics’ plasticizing and product quality.
1.Plasticizing pressure:(Back Pressure) While using screw injection molding machine, Pressure that melt on the top of screw experiences when screw rotates back. Is called plasticizing, also known as back pressure. It’s adjusted by the overflow valve of hydraulic system. During injection molding, Keeping the screw’s rotate speed same, increasing plasticizing pressure will raise melt temperature and lower plasticizing speed. Besides, increasing plasticizing pressure usually can keep melt temperature and color material’s mixing uniform, and expel airs from melt. In general, plasticizing pressure should be as low as possible under the precondition of making sure product qualified. Its specific value varies from the plastics’ types, but it often doesn’t exceed 20kg/cm2.
2.Injection pressure:
in the current production, injection pressure for almost all injection molding machines is subject to the pressure (calculated from oil circuit pressure) that plunger or screw top forces on plastics. The function of injection pressure in injection molding is to protect plastics from flow resistance from feed cylinder to cavity, offer the velocity for melt to fill mould, and compact melt
C.Forming Cycle
The time that one injection molding process takes is forming cycle, also known as molding cycle. Actually it includes the following parts:Forming cycle:
forming cycle directly affects labor productivity and equipment utilization rate. So, during production, when quality is ensured, try to shorten every related time in molding cycle. In whole molding cycle, injecting time and cooling time are the most important ones. They have a decisive impact on product quality. Fill time in injecting time is directly inversely proportional to fill rate. In production, mold filling usually takes 3-5s.
Pressure-holding time in injection time is the pressure time for plastics in cavity. It accounts for a large proportion in the whole injection time. It usually takes 20-120s (specially thick product can reach to 5 – 10 minutes). Before the melt around gate freeze, the pressure holding time has affect on product dimensional accuracy. But no affect after that. Pressure-holding time also has a most favorable value. We already know it depends on material temperature, mold temperature, and size of main runner and gate. If size of main runner and gate and process conditions are normal, it’s usually subject to the pressure value with minimum fluctuation range of product shrinkage. Cooling time mainly depends on product’s thickness, plastics’ thermal property, crystallization property, and mold temperature. The end of cooling time should base on no changes while product demoulds. Cooling timeline is usually between 30s and 120s. Cooling time needn’t be too long. This not only reduces production efficiency, but also leads to difficult demoulding. What’s worse, it may cause demoulding stress if forcibly demoulding. Other time in molding cycle is related to whether the production process is continuous and automatic and its degree.
We are glad to answer any questions or concerns about the plastic injection mould you are going to buy.
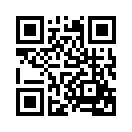
- Name:
- Mr.Zeng
- Tel:
86-571-86433485
86-137-32202800
86-189-58129996
- Email:
- sales@fridgtec.com
- WhatsApp:
- https://wa.me/8613732202800
- Skype:
- Skype:hzpkrichz
- Address:
- Rm 910, Baideli Bldg, No.519, Gonglian Rd,Binjiang, Hangzhou,China