Daily maintenance for plastic injection moulds
- Company should keep a detailed record of Plastic Injection Mould Operation, including its usage, maintenance (lubrication,cleaning, rust protection) and damage. According to these, which components are damaged and the degree of wear will be found. These will offer information for discovering and solving problems, molding technological parameter, and product material, to shorten mould trail time and improve production efficiency.
- Customers should test mould’s all functions and measure the dimension of molded plastic parts, when injection molding machine and mould are under normal operation conditions. The information can confirm the existing state of mould, help to find out damages in cavity, core, cooling system, and parting surface.According to information offered by plastic parts, the damaged state and maintenance about mould can be judged.
- Focusing on tracing and detecting the important components: the function of ejection and guiding components is to ensure the mould open and close movement and plastic part’s ejection. If any of them get stuck, it will cause production halt. So moulde jector pin and guide pillar should often be kept lubricating (choose mos tsuitable lubricating agent). Check whether ejector pin and guide pillar have any deformation and surface damage at fixed period. Once found, they must be timely replaced. After finishing one production cycle, paint professional anti-rust oil on mould working surface, moving, and guiding components.Especially attention should be paid to protection for mould bearing portion with gear wheel and gear rack and elastic strength of spring mould, to make sure it always in the best working state. Over production time, scale, rust, sludge and algee are apt to settle on cooling channel, diminishing cooling runner section, narrowing cooling channel, greatly reducing heat exchange between coolingliquid and mould. This will increase company’s production cost. So the runner’s cleaning should be brought to the forefront. For hot runner mould, maintenance for heating and control system will prevent the occurrence of production difficulty, so it’s particularly important. After finishing every production cycle, band-type heater, bar-type heater, heating probe and thermocouple onmould should be measured by Ohmmeter. If there are any damages, they need bechanged timely. Compare with the mould resume, and keep records, so as to find problems timely and take corresponding measures.
- Focusing on mould surface maintenance. It has a directly affect on product’s surface quality. The key point is to prevent corrosion, so it’s very important to choose a suitable, high quality, and professional anti-rust oil. After finishing mould productive task, choose different ways to carefully clean residue in inner of injection molding based on different plastics. Use copper bar, copper wire and professional mold cleaning agent to clean the residue injection and other sediments in mould and then make air drying. Never use solid objects like iron wire and steel rod to clean, so as not to scratch the surface, If there is anyrust caused by corrosive injection, use grinder to grind and polish, paintprofessional antirust oil, and then store mould at dry, cool, and dustlessplace.
QRCODE
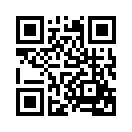
CONTACT
- Name:
- Mr.Zeng
- Tel:
86-571-86433485
86-137-32202800
86-189-58129996
- Email:
- sales@fridgtec.com
- WhatsApp:
- https://wa.me/8613732202800
- Skype:
- Skype:hzpkrichz
- Address:
- Rm 910, Baideli Bldg, No.519, Gonglian Rd,Binjiang, Hangzhou,China
Clients
E-mail Subscriptions:
subscription