Applications of Electroplated Plastics
According to Global Market Insights, the automotive industry is still the predominant user of plastic on plating technology (79.2%), followed by domestic fittings (plumbing; 9.9%) and electrical/electronics (7.7%). Let’s take a look at some of the more common plastic plating applications in each of these industries.
Automotive
Global Market Insights indicates that polymers now account for approximately 15-20 percent of the total weight of interior and exterior car parts. In addition to the lighter weight, plastic parts provide additional design flexibility. The ability to mold and bend plastic into just about any shape gives engineers a wider range of options to develop vehicle styles that differentiate their company’s products from those of the competition. Manufacturers of OEM and aftermarket parts are also making widespread use of plastic plating.
As mentioned, nickel plating is now widely used to provide a bright, chrome-like finish on a variety of plastic car parts. According to the Nickel Development Institute, the largest application of nickel plating on plastics in the automotive industry is for decorative purposes to enhance the appearance of interior and exterior parts such as grilles, wheels, light bezels, emblems, gear shift knobs, door handles and bumpers. In some instances, a chromium-nickel alloy is used instead of pure nickel.
Nickel electroplating and electroless nickel plating can also provide functional benefits for auto manufacturers. The nickel coating can enhance the corrosion and wear resistance of certain plastic parts while also increasing lubricity, which is the ability to reduce wear that results from friction.
Electronics
The Nickel Development Institute states that electrical applications represent only a small portion of the market for plating on plastics. However, the plastic plating process does play a critical role in many electrical and electronics manufacturing procedures. In terms of decorative applications, nickel and nickel-chromium plating is used to enhance the appearance of the plastic trim on computers and mobile phones, as well as the various control knobs, switched and buttons on a wide range of home electronics and electrical appliances.
In terms of functionality, plating is used to make non-conductive plastic surfaces electrically conductive. In addition, plating provides a productive coating on electrical parts that are handled frequently or exposed to environmental conditions that could cause premature wear. The development of heat-resistance plastics has created a need for the nickel plating of connector blocks to enable direct soldering on their surfaces. Additionally, electroplating can play a key role in the production of circuit systems that feature interconnecting paths.
Plumbing
The use of plastic plumbing fixtures as a lightweight, inexpensive alternative to brass has created a demand for effective plating on plastic techniques. While the first plastic plumbing fixtures were typically made of colored plastic, the demand for brighter, shinier kitchens and bathrooms have helped pave the way for the use of metal-plated plastic products as a more viable alternative. Plated plastic plumbing products provide additional design possibilities and greater flexibility when compared to brass and offer hygienic benefits. The quality of plastic plumbing fixtures has continued to improve over time, too.
While nickel-plated plumbing fixtures can provide the desired aesthetics for many homeowners, applying a gold finish over the nickel coating can meet the needs of those who want a more elegant, upscale look for their bathrooms and kitchens.
Recent Plastic Plating Developments
Plating on plastic is still a work in progress, and new techniques continue to evolve. One recent development is a double layer nickel system featuring a semi-bright nickel coating underneath a bright nickel topcoat, which provides significantly enhanced corrosion protection. Another key innovation is a microdiscontinuous chromium system that increases the corrosion resistance of nickel/chromium deposits. Using these two techniques in tandem provides superior corrosion protection in extreme environments.
Tremendous strides have also been in the development of plastic resins that are used in conjunction with electroplating. The formulation of various ABS and polycarbonate blends has resulted in stronger plastic materials that also feature excellent ductility after plating. The latter characteristic is especially valuable in automotive industry applications in terms of facilitating the recovery of the plastic material after impact.
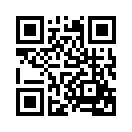
- Name:
- Mr.Zeng
- Tel:
86-571-86433485
86-137-32202800
86-189-58129996
- Email:
- sales@fridgtec.com
- WhatsApp:
- https://wa.me/8613732202800
- Skype:
- Skype:hzpkrichz
- Address:
- Rm 910, Baideli Bldg, No.519, Gonglian Rd,Binjiang, Hangzhou,China